“怎样才能再更小?”在过去一整年里,这是位于信息对抗总体部江宁园区A5楼某个不起眼的角落,某群不起眼的人最常提出的问题。
谈起信息对抗总体部产品部的各项独门绝技,“针对封装器件的一系列神操作”这一项不得不说:
数十个甚至更多数量的焊点在同一时间内被精准可靠地与印制板垂直连接,搭起器件与电路板的连接桥梁;而当需要拆下封装器件时,又能安全可靠并在同一时间内完成器件与电路板解焊,不会“伤及无辜”。
但其中有一项技术尚未吃透,即焊接技术中控制焊点的空洞率。业界IPC准备规定的空洞率是不大于25%,而集团公司的标准是不大于15%。
产品部焊接的器件焊点空洞率尽管满足了要求,但仍具有提升空间。“怎样才能再更小?”基于这一点,产品部SMT班组迅速成立了“精雕细琢”QC小组,专门来攻克这一难题。
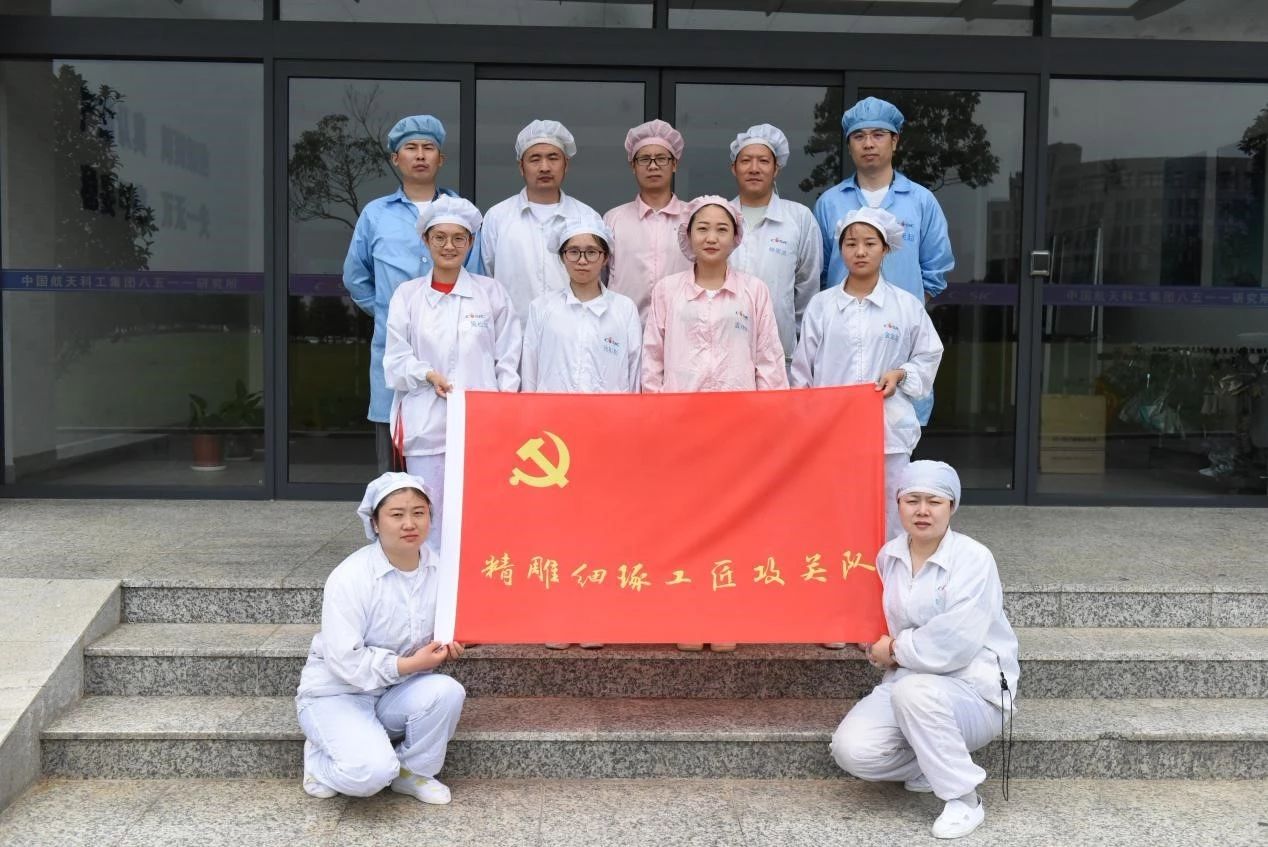
产品部副主任包杰多次组织讨论,反复研究、优化方案、策略及实施细则;刘杨豪在组织实施方案深度细化,成形并完善报告内容的同时,多次奔赴上海与IBL工程师咨询交流,搜集其他兄弟单位的经验;王民超、刘志添等主力成员在软件参数、硬件参数方面进行了大量正交试验及检测分析;机加工段的孔勇密切配合,对硬件参数不断进行优化。在这过程中,特别是当试验未做完需要加班时,大家不抱怨不放弃,挂在嘴边最多的依然还是“怎样才能再更小?”
功夫不负有心人,随着多种参数的细分及排列组合,空洞率一步一步降低,QC小组终于找到了最合适的参数组合,达到了将BGA焊点空洞率降低至低于15%的成绩,产品部又成功在工艺技术上取得一项新突破!
经过近一年的努力,也换来了沉甸甸的荣誉——“精雕细琢”QC小组获得了航天质量协会的QC小组优秀奖!
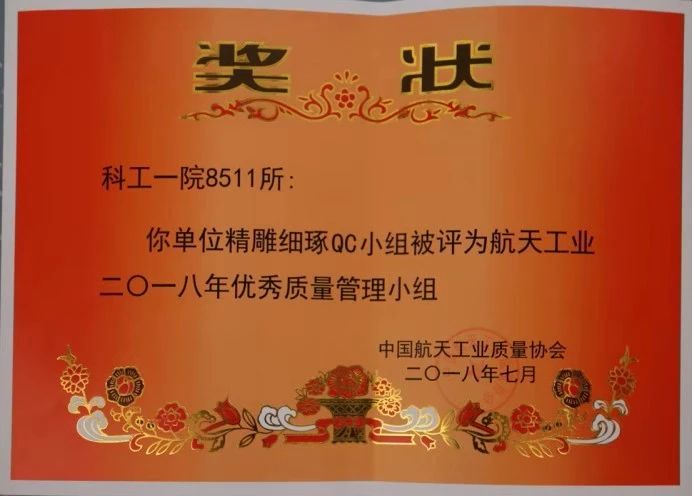
当然,这只是QC小组的第一步。军工产品质量关乎成败,他们任重道远、砥砺前行,将会朝着行业的标杆不断奋进! |